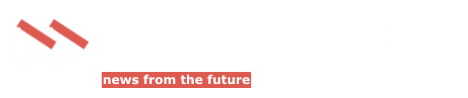
YOUR LATEST GADGET HAS ARRIVED – BY EMAIL
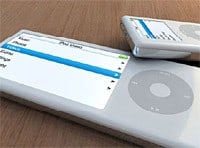
Apple's Nanofax creates digital consumer products at home
- Dateline
- 5 January 2012
At the Consumer Electronics Show in Las Vegas today, Apple’s designers unveiled their latest strategic innovation. Dubbed the nanofax, this device is essentially a three-dimensional ink-jet printer that can assemble items molecule by molecule from electronic blueprints.
Now you can shop on the internet, select and pay for your items online, and receive the ‘product blueprint’ by email. Simply clicking ‘print’ will prompt your nanofax to print the product right there and then.
At this stage the nanofax can only handle small items made from polymers, silicon and certain metal alloys – so you can’t order a digital pizza; that still has to be delivered by the pizza guy.
A battle is already looming between the nanofax and DNA construction. Chinese biotech researchers are working on organic molecular assembly kits that will let you ‘grow your own’ electronic products.
Apple clearly wants to be a leader in both of these consumer markets.
ANALYSIS >> SYNTHESIS: How this scenario came to be
Fax me an iPod Extreme
In the early days of 3D printing, scientists borrowed from commercial inkjet printing technology to create solid objects – building them up layer by layer on special substrates with microscopic droplets of powders and bonding agents.
This process was slow and expensive, but soon advanced in leaps and bounds. The most lucrative market for 3D printing was initially the rapid prototyping of product concepts. Having been designed and modeled on computer systems, it was a simple matter to output the data on a 3D printer and receive a full-scale prototype, and in some cases even a working component.
Another obvious niche for this type of assembly was the production of flat panel displays and printed circuits. Multi-layer and 3-dimensional circuits are particularly suited to piecemeal layering, especially for prototypes, test circuits and short-run job lots. But once LCD display panels could be reliably produced pixel by pixel on large format ‘printers’ it heralded a breakthrough for the manufacture of high definition displays on a variety of flexible substrates – and sized to order.
Manufacturers soon realized economies of scale with mass produced products that by design were ideal for layered micro-assembly. As bubble-jet technology matured, ink droplets measured in microns could be precisely placed, even blended from several colors of varying intensity – all the controls are digital. So too could microscopic quantities of designer molecules be precisely positioned and blended with others to build, molecule by molecule, a composite layer of circuitry and functional packaging.
In a parallel and separate development, scientists formulated a means of creating nano-scale circuits and transistors by bonding metallic molecules to strands of DNA and tiny microbes – living organisms, that by their natural propensity to connect and replicate could be cajoled into creating structures and useful linkages, even networks, that could be turned into components for devices and products. Even better than designing and assembling, bit by bit, the finished article – simply genetically code the design and the item will ‘grow’ into a completed product.
The battle is on for the production process of the future.
2003: Print up a prototype
Three dimensional printing becomes a viable method of creating computer designed prototypes.
At the same time, scientists create microscopic ‘circuits’ using DNA.
2005: Circuits, displays and clothes
Printed circuits can be manufactured on a special printer. Flexible displays are printed up with liquid crystal deposits on a pixelated base. Samsung announces efforts to reduce costs of LCD panels even further by manufacturing them with inkjet printing and using a sequential LED backlight to avoid the need for color filters.
Dutch company ‘Freedom for Creation’ together with designer Philip Delamore at London College Fashion, use existing 3D inkjet technology to print the world’s first nylon dress. The current printer costs around US$ 40,000 – within ten years this cost is set to drop more than 90%.
2007: Electronic papers hit the streets
Bendable dot displays, or thin flexible electronic displays known as E-Paper, finally become commercially available. Although these operate initially with shades of gray, full colour versions are imminent. LG Philips is instrumental in the production of E-Paper.
2010: Designer molecules come of age
Buckyballs and carbon nanotubes are old hat. Scientists create a range of specialized nano-particles that are essentially synthetic molecules – combinations of atoms and ions that are put together in precise atomic quantities so that they exhibit particular physical and chemical properties. Because they are microscopic particles, reservoirs of these designer molecules flow like liquid, and are easily used to replace inks in print-heads and cartridges. Blending different quantities of these particles in various combinations with electrostatic fields builds semi-conductors and polymers – construction at the molecular level.
2011: Printable genes
Scientists turn microscopic printing technologies into genetic modification tools. By using DNA fragments, bacteria and other microbes, and enzymes instead of inks and powders, a plethora of nano-scale ‘factories’ and device components are produced in laboratories in South East Asia. Chinese biotech researchers are soon leading the field in this form of ‘organic manufacture’, while the West debates the ethics of turning organisms into machines.
2012: Nanofax first to market
Apple surprises the market with a whole new product strategy (in typical Apple style they call it ‘Home Delivery’) and launches the nanofax, a US$ 400 device for the home or small business – even individual entrepreneurs can invest in a nanofax, download and produce products and sell them to neighborhood customers.
A whole new method of product distribution is born. This is mass-customization taken the lowest possible point. It will enable any middle-class woman to print shoes just for the evening or a new mobile phone for a friend’s birthday gift.
But, in parallel, organic manufacture is racing ahead and bound to challenge this technology. Will DNA construction prove to be the ultimate cost-saving method of converting designs into commercial products, or will ‘printed’ products dominate the market for decades to come?
Links to related stories
- MindBullet: PRINTING - THE FUTURE OF MANUFACTURING (Dateline: 17 June 2012, Published: 10 June 2004)
- MindBullet: GROW YOUR OWN PHONE OR PLAYSTATION (Dateline: 3 April 2021, Published: 17 March 2005)
- New printer produces 3D objects on demand - Gizmag 3 January 2006
- 'Gadget printer' promises industrial revolution - New Scientist 8 January 2003
- Micro-organisms may be turned into nano-circuitry - New Scientist 6 October 2005
- 3D printer to churn out copies of itself - New Scientist 18 March 2005
Warning: Hazardous thinking at work
Despite appearances to the contrary, Futureworld cannot and does not predict the future. Our Mindbullets scenarios are fictitious and designed purely to explore possible futures, challenge and stimulate strategic thinking. Use these at your own risk. Any reference to actual people, entities or events is entirely allegorical. Copyright Futureworld International Limited. Reproduction or distribution permitted only with recognition of Copyright and the inclusion of this disclaimer.